5 Effective Solutions for Different Concrete Problems
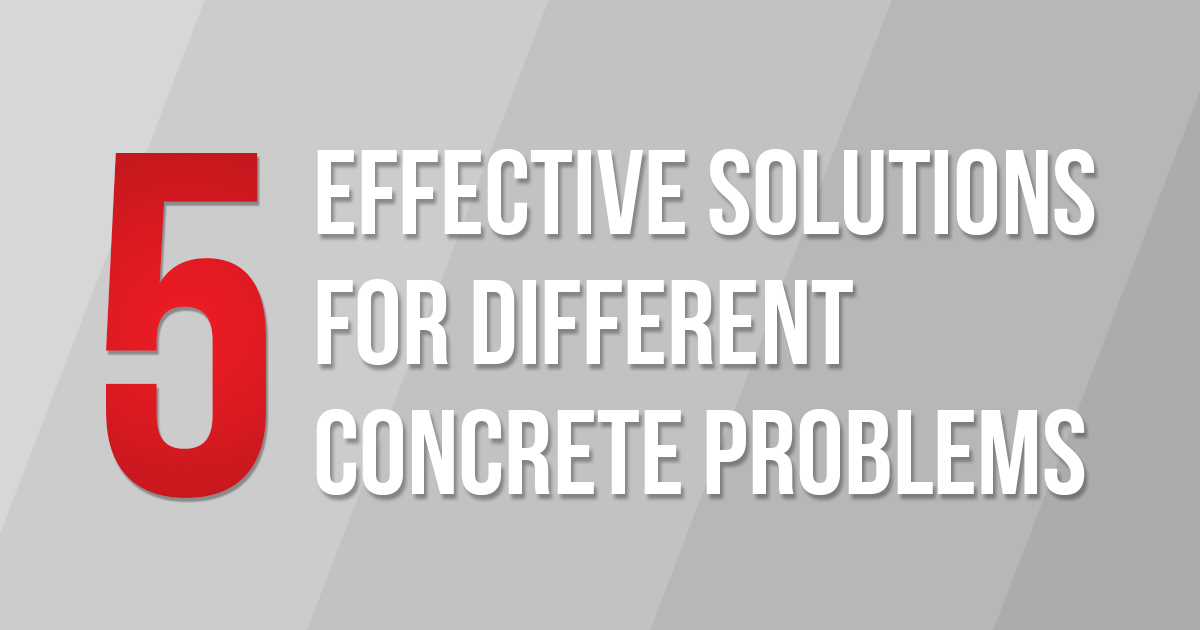
There are always certain challenges to overcome when it comes to deciding which concrete coating or polishing option is right for different workspaces. While many cases are relatively straightforward, there are certain instances that require creative solutions that stand up to unique business or personal needs. The following are five examples of different concrete coating or polishing solutions for different concrete problems.
Concrete Coating or Polishing Solutions for Unique Business Needs
Problem 1
A Parts Department was moving into a 2000-square-foot space featuring a significantly distressed floor. The existing concrete was rough and had noticeable voids. The company didn’t want concrete coating, due to heavy foot traffic. They needed an extremely durable solution that would stand up to daily wear and tear.
Solution 1
A mechanically polished concrete floor was the correct solution in this case. However, the voids and defects in the existing floor needed to be addressed first. To fill the voids, the floor was skim coated with quick-drying polycrete. The floor was then mechanically polished. This process created a smooth, dense, virtually maintenance-free floor. It was also comparatively inexpensive compared to coatings in this particular situation.
Problem 2
For the past few decades, a large shop was used to restore classic muscle cars. Recently, the decision was made to only use this shop as a showroom to display these restored cars. Of course, the shop floor showed obvious signs of the years of restoration work. Instead, the client wanted an attractive and light-reflecting floor to show off his hard work.
Solution 2
We decided on using a hybrid polyurethane. This concrete coating solution is durable and won’t delaminate over time. It can also be easily repaired in the future. Specifically, we used a light gray hybrid polyurethane, with black and white flakes. These flakes successfully camouflage any flaws and help hide dust. The finished floor reflects light beautifully and helps show off the cars. Plus, it cleans up very well.
Problem 3
A manufacturing and processing center has a room used to thaw items in water-filled vats. Once thawed, valves on these vats are opened and water freely flows out onto the floor. The constant flow of water caused the existing floor to be quite slippery. Plus, the temperature of the room also led to occasional ice build-up. On top of this all, the floor is cleaned daily with 140-degree water, and fork lifts are used to move the vats around. So, in summary, this company needed an anti-slip floor capable of withstanding thermal shock and forklift traffic.
Solution 3
Durable polycrete was used in this case. Approximately 800 pounds of quartz crystals were then broadcast to refusal by hand. After curing for around 16 hours, the leftover quartz was scraped off, and a polyaspartic top coat was used to encapsulate the quartz. This top coat is extremely durable and cures fast. Thus, it allowed the company to resume normal activity in a short timeframe. This unique concrete coating option ultimately provided traction, durability and the ability to stand up to extreme temperature change without fracturing.
Problem 4
A manufacturing facility wanted concrete coating in a 3000-square-foot space. They wanted it to look nice for clients, while also withstanding moderate-to-heavy foot traffic and forklifts. They also needed it finished quickly.
Solution 4
After the last shift of the day, we started work. We decided on a polyaspartic coating, with a light aggregate (black and white flakes). The entire process included grinding, prep work, coating, applying the aggregate to refusal, cleaning and finishing with a top coat. By the very next morning, the client was able to resume work on their attractive and durable floor.
Problem 5
Like many older buildings, an area college has terrazzo floors. Historically, these floors were topped with a heavy sealer and three to four coats of wax. This method requires constant, regular maintenance. In fact, they need to be completely stripped every two years. The client just did not have the manpower to properly care for their existing floors.
Solution 5
We stripped and mechanically polished the terrazzo floors. The floors now look great and require minimal maintenance. This relatively simple solution saved the college unnecessary maintenance time and manpower.Every company has a unique problem when it comes to different types of concrete floorings.
...
Contact us, and we will successfully determine the right solution for your particular needs.